BMW Group Plant Regensburg has introduced an autonomous transport vehicle, advancing its digitalization and automation efforts. This driverless electric vehicle, equipped with LiDAR sensors, navigates the press plant precisely and carries up to 55 tonnes, enhancing efficiency and safety. Tobias Müller, press plant maintenance manager, highlights the benefits: “This emission-free vehicle boosts productivity, saves energy, and improves safety for our employees.”
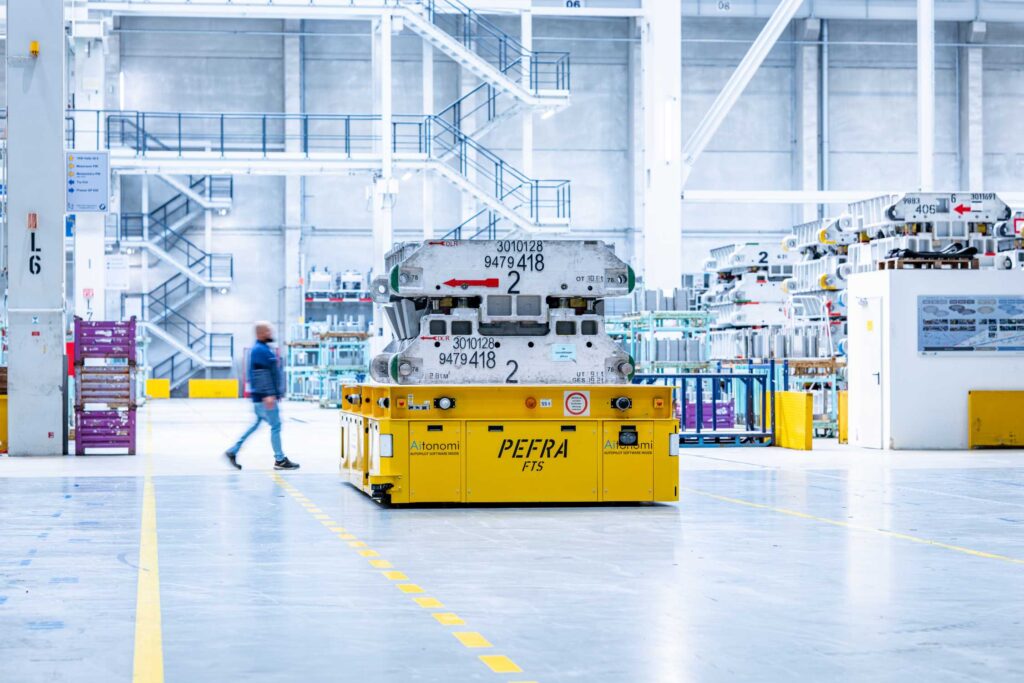
The vehicle’s LiDAR technology scans the surroundings to create a 3D image, allowing accurate and safe navigation. This innovative solution, unique to Regensburg, is part of BMW’s digital and intelligently connected manufacturing environment, the BMW iFACTORY. The plant processes about 1,100 tonnes of steel daily, producing 131,000 pressed parts for various body components.
A notable feature of the Regensburg plant is its closed recycling loop. Approximately 80,000 tonnes of offcuts are recycled into secondary steel each year, reducing CO2 emissions by 160,000 tonnes annually. Secondary steel generates two tonnes less CO2 per tonne than primary steel production, demonstrating BMW’s commitment to sustainability.
Introducing this autonomous transport vehicle marks a significant advancement in BMW’s logistics solutions, showcasing the potential of autonomous technology in industrial settings. As BMW Group Plant Regensburg continues to innovate, it sets a benchmark for sustainable, efficient, and safe manufacturing processes in the automotive industry.